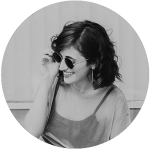
A variety of factors can damage concrete surfaces, the most common cause being regular wear and tear. Other factors include fire, seawater damage, stress, etc.
![Epoxy Cement Guide 101 [How to Repair Concrete with Epoxy] Epoxy Cement Guide](https://homesthetics.net/wp-content/uploads/2022/01/Epoxy-Cement-Guide-1.jpg)
Naturally, there are several different routes that you can take when going for concrete repair. The use of various techniques and methods also depends upon multiple factors.
Some of such factors that you need to consider before selecting the repair method include how deep the crack is, the size of the area to be repaired, time available, etc.
There are several ways to set about the process of concrete repair. Epoxy injection, Routing and Sealing of cracks, Drilling and Plugging, Gravity Filling Method, etc., are some of the methods of repairing concrete.
Here, we mention the various ways through which concrete surfaces can be repaired using epoxy, while also noting down the advantages and disadvantages of different techniques.
So, let’s get down to business.
Epoxy Cement Guide 101
Understanding Epoxy Cement Repairs
Using epoxy to repair damage in concrete is one of the popular techniques that you can use. The standard epoxy that is generally used for a wide variety of applications is a thermoset plastic. It includes a resin and a hardener.
The epoxy cement, on the other hand, also includes coarse aggregate with sand. These components ensure that the epoxy cement creates a waterproof coating that prevents further damage to the surface.
There are multiple ways in which you can use epoxy cement to repair any damage in concrete. In some instances, the procedure is simple. You can apply the epoxy injection directly to the crack to fill it up.
However, depending upon the location of the crack, the process may differ. You may require additional steps to ensure a complete repair. Alternatively, other techniques and methods might be more appropriate for fixing the damage.
Benefits Of Using Epoxy Cement For Concrete Repairs
Using Epoxy mortar or cement offers several advantages for repairing concrete surfaces. Some of these advantages include:
-
Provides High Durability
Repairing concrete surfaces such as floors using epoxy ensures that these surfaces become tough and very durable. Epoxy hardens as it dries while retaining its flexible nature. As such, it can easily absorb shocks and vibrations that hit the surface.
-
Reasonably Simple Application
In comparison with other concrete repair methods, the application of epoxy cement is a less cumbersome process. In many cases, you do not even require the assistance of a contractor and can complete the process yourself efficiently.
-
Time-Saving
Using epoxy cement to repair cracks in concrete is less time-consuming than other methods. The straightforward application process requires you to use the epoxy after cleaning the surface to be repaired.
-
Cost-effective Solution
Funding concrete repairs are generally too expensive for many people. Using epoxy cement is an ideal method that gets the job done without needing to break the bank. Additionally, undertaking the repair process without hiring a contractor also helps in saving money.
-
Suitable For Interior And Exterior Surfaces
You can easily use the epoxy repair method on all concrete surfaces, both indoor and outdoor. The cement works just as well in both conditions without being affected by the elements. Multipurpose or All-Purpose Epoxies are also available for use on a wide range of surfaces.
-
Prevents Further Damage
The timely application of epoxy cement to repair minor cracks in concrete can help you save a significant amount of money. This adhesive holds tightly to the surface, preventing further deterioration while also acting as a waterproof barrier.
Suitability of Epoxy Cement For Different Types Of Repairs
Before deciding which epoxy material is ideal for repairing your concrete, you should first check the compatibility of the glue with the surface. Not all types of epoxies work well with concrete.
Additionally, the type of damage that needs to be repaired also determines which material and technique for repairing would be most effective.
For surfaces that have cracks passing entirely through, epoxy injections are an easy way to repair them. The epoxy resin in such a case should be very fluid to reach the interior of the material.
However, this method of repairing concrete is only applicable if further movement is not possible. If there is a possibility of further shifting within the concrete, other techniques are more suitable.
Keep in mind that epoxy injection for concrete repairs is not suitable for extensive cracks. Similarly, structural cracks should also not be repaired using this method. In case of cracks that have water inside, use water-resistant epoxy cement for best results.
Using epoxy for repairs is not a practical solution in scenarios where cracks appear in concrete due to corroded steel. This is because the epoxy will not stop further decay of the material, and more cracks will continue to appear. For fixing large cracks, separate repair kits are available on the market.
Epoxy Cement Compared To Other Repair Materials
Epoxy cement is one of the several popular materials available for repairing cracks in concrete surfaces. Alternatives include Epoxy Mortar, Urethane Cement, etc. There are subtle differences between these repair materials, and they serve different purposes.
Similar to craft resin, epoxy cement also includes a resin and hardener. The mixture is easy to apply and provides durability as well as water resistance. It is available in different shades, making it suitable for different types of concrete. It also works well with other materials such as urethane cement.
In the case of epoxy mortar, it also contains epoxy, just like epoxy cement. This property makes both materials water-resistant and highly durable. They also have similar results, such as preventing corrosion, repairing tiles, etc.
The difference between the two materials lies in their composition. While epoxy cement contains a significant portion of a powder-like substance that acts as a filler, epoxy mortar contains sand-like material for the same purpose.
You can also get an epoxy putty, which contains the filler substance but offers a thicker consistency. It is suitable for use as a putty-like adhesive to fill space. However, epoxy putty serves a different purpose than epoxy cement and epoxy mortar.
Another option for repairing cracks in concrete is Urethane Cement, which is also called polymer concrete. Polymer concrete comprises urethane mixed with an aggregate and standard cement that is ideal for creating waterproof surfaces.
Unlike epoxy mortar, it is possible to use urethane cement along with epoxy cement. The mixture not only creates a strong bond but also offers scratch resistance and durability.
Deciding which material to use to repair concrete surfaces depends on your particular requirements. Factors that need to be considered include material compatibility, type of damage, cost, water resistance, etc.
The Repair Process
Despite being an overall simple process, the process for repairing cracks in concrete requires excellent care. Several steps need to be followed in the correct order to get the best results. Here, we explain the entire process of how to go about repairing concrete surfaces using epoxy.
Before starting the epoxy crack repair process, ensure that this process is suitable for the scenario. One of the ways to determine this is to use a sounding hammer which will help make a correct assessment of the concrete.
Understanding the width and depth of the crack is vital before deciding on the method of repair. Portable crack scopes or plastic crack cards will help you determine the quantity of epoxy required. Generally, more minor repairs lead to more waste as more material is needed for flushing the gun than for filling the cracks.
Another thing to remember is that weather plays a significant role in how effective and quick the crack repair process is. In cold weather, cracks may contain frozen water, which increases the effort required to fix it.
Cold weather also increases the time that the epoxy requires to get cured. In such circumstances, the injection process must be slow, and the seal should be left on for longer. Ensure that the coating has the correct dew point to prevent any dew from getting trapped underneath the epoxy.
If the temperature falls below 35°F-40° F, the epoxy will go into a dormant state. This issue is not something to be worried about, as it will start to cure again once the temperature increases. To speed up the curing process, use an external source of heat.
-
Required Tools
It is necessary to have the right tools and supplies at hand when starting a crack repair process. Some of the tools required include a disposable surface for mixing the epoxy, a utility knife, and a putty knife for mixing purposes.
Safety gloves, goggles, and face masks are also recommended to prevent the material from getting into your eyes or hands. If possible, work in a properly ventilated area that has good airflow.
-
Preparing The Concrete Surface And The Epoxy
The damaged concrete surface that needs to be repaired should be appropriately prepared before starting the process. This process requires cleaning the surface using either wire brushes or a high-pressure water cleaner. When using a pressure water cleaner, make sure it has at least 5000 PSI for best results.
A clean concrete surface will ensure that the filler bonds properly to the damaged surface.
Let the surface dry completely before starting the process. If there is a time constraint, tools such as air dryers can speed up the drying process. Also, avoid using mechanical devices for the cleaning process as it can lead to further debris falling inside the crack.
The standard procedure for repairing cracks in concrete involves widening the gap into a “V” shape. This V shape provides a more resistant finishing after the application of the epoxy.
In case the epoxy to be used for application is too thick, it requires thinning before use. Preheating the epoxy before mixing is an effective way to thin it out. Other methods include storing it in heated rooms or adding a lightbulb to the injection pump.
Keep in mind that the temperature changes will also affect the curing time of the epoxy after it has been mixed.
-
Installation Of Ports
Ports are used to inject epoxy into the concrete, which helps eliminate the need for drilling. There should be at least two ports that need to be spaced out properly for the correct application of the epoxy.
The ports should be 8 inches apart and installed along the crack in the concrete. After installing the ports, the top of the crack needs to be sealed. Use an epoxy paste along the length of the crack to cover it with the help of a putty knife.
Leave the paste to dry for about 30 minutes, as it needs to be stable enough during the epoxy injection. Keep in mind that the temperature of the concrete determines the adhesion and seal of the epoxy.
-
The Epoxy Injection Process
Mix the two-part epoxy properly until onto the disposable mixing surface there are no visible streaks in the mixture. In the case of a readymade epoxy, there is no need for mixing, and you can directly get down to the injection process.
Start the injection process by first injecting the crack repair epoxy into the lower port in the concrete. Continue to inject the epoxy until either it flows out of the next port or stops flowing. While working on horizontal cracks, start at the broadest part of the crack.
During the injection process, closing the second port might be beneficial for filling up the gaps below the concrete surface. Once the epoxy stops flowing, remove the port and proceed to the next port.
Repeat the process with all the ports until the entire crack is filled. In case the epoxy has hardened at a port, proceed to the next one. Just keep applying a steady constant pressure during the injection process to prevent uneven filling or voids.
Once the entire crack has been filled, remove the ports and use epoxy to seal up the top of the crack. The temperature determines the curing time of the epoxy. To speed up the curing process, use a moderate heat supply in cases where there is a time constraint.
There are various tools and methods to increase the temperature for a faster curing process. Use a heat gun, preheat the epoxy before application, use baseboard heaters or warming blankets to achieve the desired results. Thicker areas will get cured faster as epoxy also emits heat by itself during the curing process.
Keep in mind not to exceed 300° F while heating as epoxy tends to start deforming at that temperature. High temperatures in summer can also affect the durability of epoxy.
-
Cleaning Up And Storage
Once the job is complete, it is essential to clean up the epoxy from the workspace and tools. MEK or acetone is an excellent product for this process. For cleaning up tools or small areas, dishwashing soap and water also provides great results.
Liquid detergents or concentrated soaps are better alternatives to solvents for removing epoxy from the skin.
After the repair process, there may be some unused epoxy leftover. Only unmixed epoxy is considered leftovers as it will not cure and can be stored for future use. Store excess epoxy in airtight containers until it is needed again.
Unfortunately, water-sensitive substances such as polyurethane do not allow for such long storage periods. Either use such materials quickly or dispose of them.
-
Finishing And Finalizing
In many cases, simply fixing the cracks and getting the concrete repaired is not enough. The surface needs to be adequately maintained to provide the proper appearance. Sacking is a process that will help you restore the original smooth surface of the concrete.
Sacking involves wetting the surface of the concrete and hitting it with a sack that contains a satisfactory amount of the color of the concrete. Another alternative is to paint over a fine cement-based slurry using a brush.
Epoxy Cement Repairs For Different Surfaces
Epoxy cement is a highly versatile substance that can be used to repair all types of concrete surfaces. These may include concrete floors, sidewalks, driveways, and more.
Here we will tell you how to make the best use of epoxy cement to repair such different surfaces. So let us get straight to it.
-
Repairing A Sidewalk With Epoxy Cement
The process of repairing any damage to the sidewalk depends upon the size and depth of the crack. If the crack is extensive, it needs to be enlarged first using a hammer and a cold chisel.
The process requires undercutting, which involves making the crack wider at the bottom and thinner at the top. Following this, any residue remaining in the area should be removed using a wire brush and a pressure hose. Before proceeding to the next step, ensure that the surface is completely clean.
The next thing to do would be to apply an acrylic resin glue to the surface, which should be left to dry. A pre-mixed concrete patch has to be applied to the undercut area. Use a trowel to ensure that the mixture is completely smooth before use.
Once this process is complete, cover up the cement while it is still wet until it dries up. A plastic sheet should be left over the area for at least five days for best results.
-
Repairing A Driveway Using Epoxy Cement
To repair a driveway with epoxy cement, you should start by following the same process as sidewalk repair. Remember that, unlike a sidewalk, a driveway has to bear a considerable amount of weight. Therefore, it requires more strength.
To ensure that the driveway has enough strength, use a gravel composition using sand, cement, and gravel. First, undercut the damaged area and then apply the epoxy cement for repair.
After completing this process, repeat the steps for repairing the sidewalk. The driveway should also be left for a minimum of 5 days before using it. To get an even stronger surface, add epoxy to the mixture.
-
Repairing Hairline Concrete Cracks with Epoxy
Unlike larger and broader cracks, hairline cracks often go unnoticed, which leads to further damage if not dealt with timely.
The process to repair hairline cracks starts with the creation of a paste by combining cement and water. Moisten the crack that needs to be fixed for at least 4 hours before beginning the repair process.
This process makes it easier to apply the paste once the surface has become completely dry. Use a pointed trowel to apply the paste to the crack.
The concrete crack repair epoxy is also suitable for this purpose. It is a Two-Part Epoxy Adhesive Paste that provides excellent results for repairing hairline cracks in concrete.
During the application process, put in a bit of weight and ensure that the paste enters the crack. After this, flatten the surface to make it smooth before leaving it to dry for about 2 hours.
Similar to the above procedures, cover the area with a plastic sheet for five days. Remember to lift the sheet and sprinkle a little water on the surface every day. The surface becomes perfectly ready for use after five days.
Valuable Tips for Repairing Concrete Cracks
There are several different concrete cracks, and one single repair solution does not apply to all. During the repair process, some issues tend to come up and require your attention. Some of the most common issues and the methods to deal with them are listed below:
-
- First and foremost, verify that the crack can be fixed using the epoxy injection method.
- For larger cracks, there are other methods of repairing cracks that work better.
- Always start the injection process with the lowest-pressure setting and increase the pressure as required.
- Use more epoxy injection pressure to fill up larger cracks.
- For wider cracks, it is best to fill them slowly without rushing.
- A slow filling process ensures that the epoxy is filling the crack correctly.
- Be prepared for epoxy backflow, which may result from blockage by debris, or the crack may not be continuous.
- Epoxy polymers always tend to contract and expand more than concrete.
- The property of rapid expansion and contraction should be kept in mind when working on a large crack.
- The top seal can be removed using a chisel, scraper, while a heat gun helps remove the epoxy paste.
- Ensure that you only remove the ports after the epoxy has fully set.
- The process of setting requires at least 48 hours to complete.
- In case there is a leak in the top seal, insert a crayon to stop the leakage.
- The technique of using a crayon works well only for areas with small leaks.
- If the cracks are narrow, applying a bit of caulk on the side of the crack reduces epoxy waste.
- Using caulk also helps improve the adhesion and filling of the epoxy.
Recommended Products
There are several epoxy products for repairing cracks in concrete available on the market. However, selecting the one that fits your purpose is not an easy task. There are several factors to consider, such as ease of use, curing time, flexibility, etc.
Here, we would like to mention some of the best crack repair epoxy products worth considering. The purpose of this section is to help you save time and effort while discovering products that ensure the best results. So, let us get down to it.
-
PC Products PC Concrete Epoxy Adhesive
The first product we would like to mention comes from PC Products, one of the biggest names in the epoxy industry. The PC Concrete Epoxy Adhesive is one of the brand’s excellent products for repairing cracks in concrete.
It is easy to use, moisture-resistant, and also suitable for vertical applications. This epoxy can also be used to anchor rods, bolts, and dowels into concrete and is the perfect solution for interior and exterior usage. The product has a PSI rating of 6790 which also ensures a very high level of durability.
-
Quikrete Epoxy Concrete Repair
Another product that offers excellent value for money is the Quikrete Epoxy Concrete Repair. This two-part epoxy forms a highly durable bond and is a very reliable product for concrete repair.
It also works well on vertical surfaces and is suitable for interior as well as exterior use. Also, it is a fast-drying epoxy that does not shrink and can be used on concrete, brick, stone, and similar surfaces.
Several other products are available on the market that also offer excellent results for repairing cracks in concrete. It is ideal to select the one which perfectly meets your particular requirements. Keep in mind the various factors before making the final decision.
Conclusion
As mentioned before, repairing cracks in cement using epoxy is one of the most convenient techniques available. It is also cost-effective, especially when compared to hiring a contractor to do the job.
Several products are available on the market for use in repairing cracks in concrete. Each product has its advantages and disadvantages, and selecting the right one depends upon your particular requirements.
The most important thing to keep in mind while undertaking repairs yourself is to ensure all safety measures are followed. And, in case you feel that all this is too tough to tackle by yourself, feel free to contact a professional and get the job done.
With that, we finally take our leave.
Related Articles
8 Best Basement Cement Floor Paints
9 Best Concrete Stains to Consider
11 Best Concrete Bonding Agent to Use this Year
11 Best Paint For Concrete Walls In Basement
5 Best Paver Sealers for a Wet Look of Epic Proportions
How to Color Clear Epoxy Resin [Coloring Resin
How To Fix Radiator Leak With Epoxy+ Best Radiator Repair Epoxy
Epoxy Garage Floor 101 [All You Need to Know]
Mold Release Guide + Best Epoxy Release Agents
Surfaces Resin Won’t Stick to [All You Need to Know]
Heat Resistant Epoxy 101 [A Guide for High Temperatures]
How To Mix Epoxy 101 [Measuring & Mixing Epoxy Resin Guide]
How To Harden Sticky Resin [Uncured Epoxy Solutions]